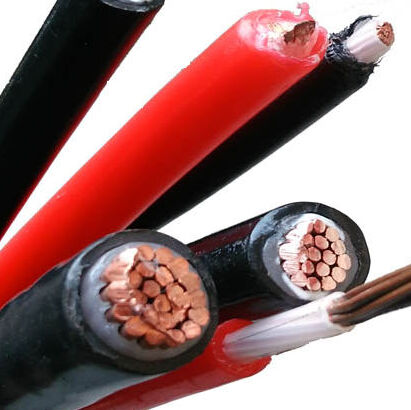
We are specialized and professional manufacutrer of kynar cables
our CP cable has been exported world wide
- the cable is used for cathodic protection , with copper conductor, kynar insulation and hmwpe sheath
CP cable packing details
loading and shipping
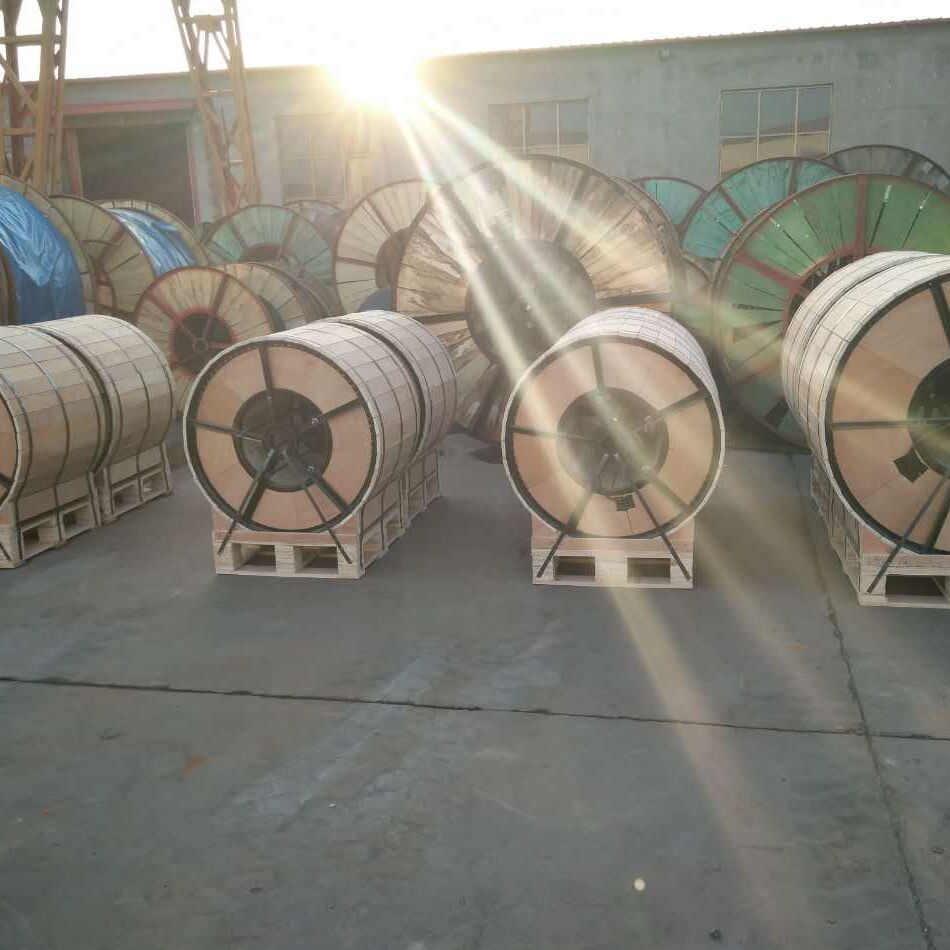
kynar hmwpe
>>>>>>contact us: sales@cablesyt.com>>>>>>>> whatsapp/wechat:+86 18931155779
Cathodic Protection Cable: Ensuring Durability and Integrity of Metal Structures
The concept of cathodic protection is a fundamental component in the preservation of metal infrastructure, particularly in corrosive environments. Central to this system is the cathodic protection cable, a specialized component that facilitates the delivery of electrical current necessary to mitigate corrosion. Let’s delve into the intricacies of this crucial element.
What is Cathodic Protection?
Cathodic protection is a method used to control the corrosion of a metal surface by making the metal surface the cathode of an electrochemical cell. This is achieved by applying an electric current from an external source, which counteracts the corrosion process. There are two main types of cathodic protection: sacrificial anode protection and impressed current cathodic protection. Regardless of the method, the cable plays a pivotal role in transporting the electric current from the power source to the metal surface that needs protection.
Types of Cathodic Protection Cables
1. Sacrificial Anode Cables: These are used in sacrificial anode systems where a more reactive metal is connected to the structure to be protected. The anode will corrode in place of the protected metal. The cable is typically made of a conductive material that can withstand the environmental conditions and efficiently transmit the current.
2. Impressed Current Cables: For systems where an external power source is used to impose a current, these cables must be capable of conducting high currents and resist corrosion, as they are exposed to the harsh environments where cathodic protection is needed.
Characteristics of High-Quality Cathodic Protection Cables
- Conductivity: The primary function is to conduct electricity, so high conductivity is essential.
- Corrosion Resistance: The cable must resist the corrosive environment where it is placed.
- Mechanical Durability: It needs to withstand installation stresses and environmental conditions without damage.
- Flexibility: Many applications require the cable to be bent or routed around obstacles, hence flexibility is a desirable trait.
- Thermal Stability: The cable should remain functional across a broad temperature range.
Design Considerations
- Insulation Material: The choice of insulation material is critical for durability and environmental resistance.
- Cable Size: The appropriate gauge of the cable must be selected based on the current-carrying capacity required.
- Jacketing: A protective jacket is often used to provide additional protection against physical damage and chemical attack.
Installation and Maintenance
Proper installation is essential for the effectiveness of cathodic protection systems. The cables need to be securely connected to both the anode (or power source) and the structure to be protected. Regular inspection and maintenance are necessary to ensure that the cable remains intact and effectively conducting current.
Conclusion
Cathodic protection cables are a vital component in the battle against metal corrosion, safeguarding a wide array of structures from pipelines and tanks to marine structures and underground storage facilities. By effectively transmitting the necessary electrical current, these cables ensure the longevity and integrity of metal assets, making them indispensable in industries where corrosion poses a significant risk. As technology continues to advance, so too does the design and efficiency of cathodic protection cables, contributing to the continued protection of our critical infrastructure.